Made in the USA Vehicle Cost: Is It Worth It?
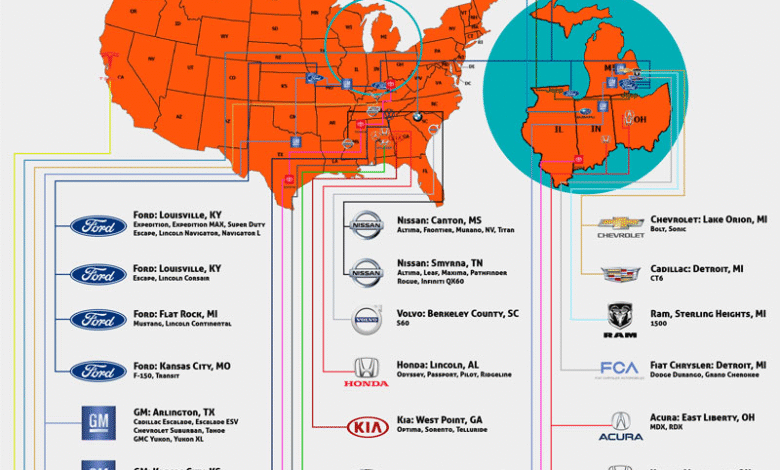
How much would a 100% ‘Made in the USA’ vehicle cost? Achieving this ambitious goal presents a complex challenge for automakers, especially amidst pressures from policies aimed at bolstering U.S. car manufacturing. While models like the Ford Expedition are assembled by American workers, many essential components still rely on foreign production, including parts sourced from Mexico that make up nearly a quarter of their makeup. The ongoing Trump tariffs impact have compelled manufacturers to localize their automotive supply chain, yet experts warn that reaching a fully domestic vehicle would drastically increase costs. Thus, the realities of achieving a truly 100% American vehicle stir significant debate among consumers and industry leaders alike, as the financial implications could deter potential buyers from fully embracing these homegrown alternatives.
The cost of vehicles manufactured entirely within U.S. borders is a contentious topic in today’s automotive landscape. This discussion touches on various aspects, including the feasibility of sourcing all parts domestically and the effects of recent tariffs imposed on foreign imports. As automotive brands strive to enhance their local production capabilities, understanding the dynamics of U.S. car manufacturing and its implications on prices remains crucial. The intricate web of the automotive supply chain reveals just how dependent American manufacturers still are on international markets for key components like semiconductor chips and wiring harnesses. As the industry works towards a more localized production model, the challenge of balancing affordability and domestic sourcing will define the future of vehicle costs.
Understanding the True Cost of 100% American Vehicles
The dream of a 100% ‘Made in the USA’ vehicle often comes with a hefty price tag. Industry experts warn that as the automotive supply chain becomes more localized, costs are inevitably pushed higher. American automakers, such as Ford with their assembly in Kentucky, face the dual challenge of rising costs while also trying to comply with increasing pressures from policymakers to utilize American-made parts. In many cases, this ambition is countered by the reality that many essential components, including wiring harnesses and semiconductor chips, are still sourced from overseas due to cost-effectiveness.
Furthermore, the complexities of U.S. car manufacturing are exacerbated by existing international trade agreements and the rising costs associated with tariffs imposed on foreign imports. Since President Trump’s introduction of 25% tariffs on imported vehicles and parts, automakers have worked to innovate their supply chains. However, even with domestic assembly plants running at full capacity, the majority of key vehicle components still come from foreign sources, raising questions about the feasibility of a truly American vehicle.
The Impact of Trump Tariffs on Vehicle Costs
President Trump’s tariffs have significantly reshaped the landscape of the automotive industry. By imposing hefty duties on imported vehicles and associated parts, the intention was clear: to encourage automobile manufacturers to rely on U.S. resources. However, the results have been mixed. While some companies have responded by attempting to localize their supply chains, the costs of manufacturing vehicles solely from American-made parts have skyrocketed. As transportation costs increase, these expenses inevitably trickle down to consumers.
Moreover, some components remain cheaper to produce abroad, making it economically challenging for manufacturers to source all materials domestically despite tariffs that create a level playing field. Take, for example, the Ford Expedition; while it’s assembled in the U.S., the reality is that up to 22% of its components hail from Mexico. Thus, while tariffs intended to foster a self-sufficient automotive industry, achieving cost-effective production remains a barrier, underscoring the broader implications of U.S. car manufacturing.
Challenges in Building a Locally Sourced Vehicle
The process of building a vehicle with 100% U.S.-made parts is fraught with challenges. Experts like Mark Wakefield from AlixPartners emphasize the intense investment and time required to develop a fully domestic supply chain. Many vehicle parts simply do not exist in sufficient quantities within U.S. borders, or they are price-prohibitive to produce at scale. Therefore, even an ambition of 90% local sourcing requires serious financial commitment from automakers, and such a move could lead to dramatic increases in vehicle prices.
As U.S. manufacturers scramble to meet the demand for American-made vehicles, consumers may find themselves facing higher sticker prices. Transitioning to vehicles that meet stringent U.S. content standards creates a complex tug-of-war between quality, affordability, and domestic job creation. For many consumers, the promise of a vehicle that embodies ‘100% American’ may come at an unattainable expense, further complicating the push for complete localization.
Why ‘Made in the USA’ Doesn’t Mean 100% Domestic Parts
The label ‘Made in the USA’ often leads to misconceptions, suggesting that a vehicle’s parts are entirely produced domestically. However, the reality within the automotive supply chain defies this simplicity. Even within models that are assembled in American factories, such as the Ford Expedition, a significant percentage of parts originate from outside the U.S. This illustrates the interconnectedness of global manufacturing and the dependencies that arise from decades of global trade agreements.
This situation underscores the challenges faced by stakeholders in the automotive sector striving for more American-made content. Estimating that vehicles are built from around 20,000 individual parts sourced from anywhere between 50 and 120 countries complicates the issue. Thus, the movement towards a fully American vehicle must still grapple with market realities, affecting consumer expectations and purchasing power.
The Future of U.S. Car Manufacturing and Costs
As manufacturers grapple with the desire to produce more vehicles domestically, the path ahead remains convoluted. Aiming for higher percentages of U.S.-made parts is viewed by many as a practical approach, targeting 75% to 80% U.S.-Canadian parts rather than an outright 100%. Vehicles like the Kia EV6 and Tesla Model 3 demonstrate that while it is possible to reach significant domestic sourcing levels, it’s crucial for the industry to navigate sustainability and affordability effectively.
Moreover, insights from industry leaders like Ford’s CEO Jim Farley indicate that while the goal of boosting American manufacturing is paramount, the transition must be gradual to avoid alienating consumers. Costs associated with switching to a more domestically sourced framework could alienate buyers who cannot afford the inflated prices that may come with manufacturing changes, possibly stunting the growth of the very American vehicle market policymakers wish to promote.
Balancing Quality and Cost in Automotive Production
Creating vehicles that are both affordable and ‘Made in the USA’ requires a fine balance between quality and cost. As American manufacturers strive to enhance their domestic production, they are inadvertently confronting the challenges posed by global competition. Many parts remain cheaper to acquire overseas, and as tariffs continue to create financial pressure, achieving this ideal balance can feel impossible. Maintaining quality standards while sourcing materials domestically presents another layer of complexity.
Automakers are thus faced with the dual task of ensuring that the vehicle they produce is up to standard while also ensuring it remains competitively priced. In this landscape, the focus on the automotive supply chain becomes critical. As manufacturers work to diversify suppliers and localize supply chains, the balance of quality and cost will determine the success of these ‘Made in the USA’ ambition and its sustainability in the long run.
Consumer Perspectives on Domestic Vehicles
Consumer sentiment is a crucial component in the discourse on U.S.-manufactured vehicles. Buyers increasingly express a preference for supporting American-made products, yet they also seek value for their money. With rising prices anticipated due to a shift towards higher domestic content vehicles, understanding the consumer perspective becomes essential for automakers. If prices escalate excessively, even with the allure of ‘100% American,’ buyers may turn to alternatives that offer better value.
The challenge lies not only in producing vehicles that are proudly American but also ensuring they remain accessible to the average consumer. Identifying ways to reduce costs without sacrificing the integrity of American jobs and parts sourcing will be essential as the industry evolves. Manufacturers who listen to consumer feedback and strike this delicate balance may find broader acceptance in the marketplace.
Regional Impacts on Automotive Production Costs
The push for more American-made vehicles has distinct regional implications that can heavily influence cost structures. As automotive plants proliferate in areas with lower labor costs, the reshaping of the automotive supply chain can yield both advantages and disadvantages. The proximity to suppliers who can provide vital components can create benefits in terms of reduced shipping costs and faster assembly times.
Conversely, regional disparities in material production capabilities can lead to variances in cost. For example, areas with high levels of industrialization may have access to lower-cost materials, while regions less developed may struggle to source competitively priced components. As manufacturers aim for higher percentages of U.S. sourced materials, understanding these regional dynamics will be critical to maintaining operational efficiency and product affordability.
The Role of Innovation in U.S. Car Manufacturing
Innovation plays a pivotal role in the evolution of U.S. car manufacturing. As automakers face pressure to produce more American-made vehicles, technological advancements can significantly ease the transition to local sourcing. For instance, advancements in materials science and automation may enable manufacturers to produce parts in the U.S. more economically, reducing reliance on foreign imports.
Moreover, by investing in research and development, the automotive sector can address some of the root causes of the sourcing challenges they face today. By automating processes and streamlining logistics, manufacturers may find that they can meet U.S. content goals without pricing themselves out of the market. This innovative spirit is critical not just for the automotive industry specifically, but also for the broader implications on U.S. manufacturing as a whole.
Frequently Asked Questions
How much does a 100% American vehicle cost compared to others?
The cost of a 100% American vehicle can vary significantly. Achieving 100% domestic content in a vehicle might raise prices by $5,000 to $20,000, due to the need for expensive local sourcing and production of parts that are often cheaper abroad.
What are the impacts of Trump tariffs on U.S. car manufacturing costs?
Trump’s 25% tariffs on imported vehicles and parts have pushed automakers to localize their supply chains, which can lead to higher manufacturing costs. While intended to encourage U.S. car manufacturing, these tariffs can further increase the costs of ‘Made in the USA’ vehicles due to limited domestic production of components.
Are there challenges in sourcing parts for U.S. car manufacturing?
Yes, despite assembling vehicles in the U.S., many parts still come from overseas. Approximately 15% to 20% of vehicle components, such as wiring harnesses and semiconductors, are difficult to source domestically, complicating efforts to achieve a higher percentage of 100% American vehicles.
Why is achieving a 100% ‘Made in the USA’ vehicle not feasible?
Achieving a 100% ‘Made in the USA’ vehicle is challenging because essential materials and components are still better produced abroad, making it economically unviable. Experts suggest that even reaching 90% domestic parts requires significant time and investment, which may skyrocket production costs.
What is the average vehicle cost attributed to U.S. car manufacturing strategies?
The rising focus on U.S. car manufacturing can increase vehicle costs. Estimates suggest that achieving higher levels of domestic content could make vehicles unaffordable, with potential price increases of $5,000 to $20,000 for cars solely made from American parts.
Which vehicles currently meet higher U.S.-made content standards?
Models like the Kia EV6 and the Tesla Model 3 are noted for achieving higher standards of U.S.-Canadian parts, typically over 75% domestic content. However, many other vehicles have seen a drop in local content compared to previous years due to increased globalization.
How does the automotive supply chain affect the cost of making 100% American vehicles?
The automotive supply chain is global, with many parts sourced from 50 to 120 countries. This complexity means that while a vehicle can be assembled in the U.S., its parts often come from abroad, making it difficult and costly to achieve a 100% American-made vehicle.
What role do American labor and manufacturing facilities play in vehicle costs?
American labor and manufacturing facilities, like Ford’s Kentucky Truck Plant, contribute to the assembly of 100% American vehicles. Despite this, a significant portion of parts still comes from overseas, affecting overall costs and the feasibility of achieving a complete ‘Made in the USA’ label.
Key Point | Details |
---|---|
Complicated Costs | Establishing a 100% ‘Made in the USA’ vehicle is a complex process influenced by global supply chains. |
Foreign Parts Dependency | Even domestically assembled vehicles use foreign parts, limiting complete U.S. production. |
Cost Increases | Experts suggest costs rise significantly as manufacturers aim for higher domestic content. |
Tariffs Impact | Aggressive tariffs have prompted automakers to localize, but full U.S. content remains impractical. |
Challenges in Sourcing | Essential components like chips and wiring harnesses are hard to source domestically. |
Projected Price Increase | Achieving 100% U.S. parts could increase vehicle prices by $5,000 to $20,000. |
Realistic Goals | Aiming for 75% or higher U.S.-Canadian components is currently seen as more achievable. |
Summary
The cost of a 100% ‘Made in the USA’ vehicle is a multifaceted issue that reflects the complexities of modern automotive manufacturing. While efforts to promote American-made vehicles are on the rise, achieving full domestic content is fraught with challenges, primarily due to dependency on foreign parts, varied sourcing difficulties, and substantial cost increases that may deter consumers. As industry experts suggest, realistic targets such as 75% domestic components seem more attainable, indicating that while the ambition for a completely American-made vehicle persists, the current economic framework complicates its realization.