Trump Tariffs: Will They Revive U.S. Manufacturing Jobs?
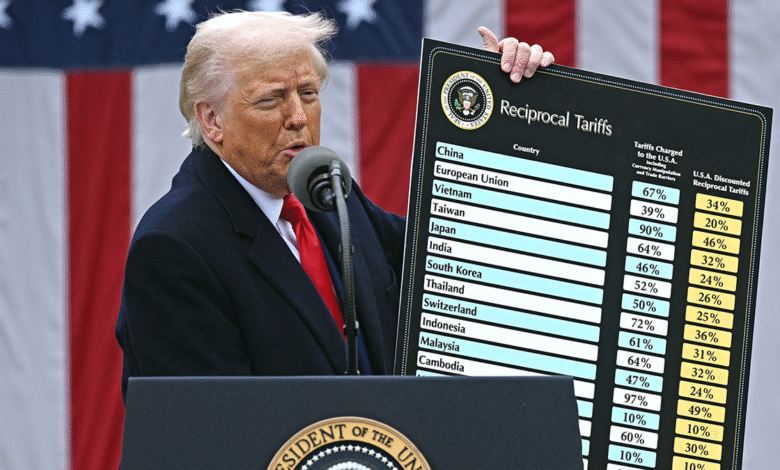
Trump tariffs have been a hot topic in the ongoing discourse about the revival of U.S. manufacturing jobs. Intended to incentivize companies to reshore operations, these tariffs are positioned as a strategy to restore a thriving manufacturing employment sector. However, an analysis by Wells Fargo suggests that the anticipated resurgence may be more of a fantasy than reality, citing the challenges posed by significantly higher labor costs. Companies find themselves navigating a tight labor market, complicating their ability to expand payrolls, regardless of the tariff incentives. As the trade war tariffs reach their highest levels since the 1940s, the prospect of a manufacturing boom seems increasingly elusive.
The protective measures implemented during Donald Trump’s administration, often referred to as trade tariffs, aim to stimulate the domestic production of goods by encouraging businesses to relocate their manufacturing bases back to the U.S. While this initiative is purported to lead to a considerable increase in production jobs, recent evaluations, such as those conducted by Wells Fargo, paint a different picture. The anticipated influx of manufacturing positions may be overshadowed by rising labor expenses and a limited workforce willing to fill these roles. Despite high-profile commitments from the tech sector to invest domestically, the reality of returning to the peak levels of manufacturing employment remains daunting. Overall, the challenge of invigorating the American manufacturing landscape amidst this policy framework is significant and fraught with obstacles.
The Challenges of Trump Tariffs on U.S. Manufacturing
Trump’s tariffs were implemented with the intention of revitalizing U.S. manufacturing by creating a stronger incentive for companies to bring their jobs back from overseas. However, the reality is that these tariffs have imposed significant costs on manufacturers, who face elevated labor costs and a shrinking workforce. According to a Wells Fargo analysis, labor market constraints are a critical barrier as the existing availability of production workers is already stretched thin. This existing pressure complicates the ability for companies to expand their operations domestically, despite the government’s attempts to stimulate the economy through trade policies.
In essence, the tariffs are designed to alter corporate strategies, but their effectiveness is undermined by the ongoing challenges in the labor market. Even with the highest effective tariff rates in decades, companies are hesitant to fully commit to reshoring. Price increases resulting from tariffs are likely to be passed on to consumers, potentially diminishing demand and further complicating job growth in the manufacturing sector. The Wells Fargo report notably highlights these economic tensions, cautioning that while policymakers aim for a manufacturing resurgence, the landscape is fraught with obstacles that stand in the way of real progress.
The Realities of Reshoring and Manufacturing Employment
The notion of reshoring jobs back to the United States, particularly in light of recent trade war tariffs, faces entrepreneurial skepticism. Wells Fargo’s analysis articulates the stark difference between desired outcomes and achievable results. With approximately 12.8 million manufacturing jobs currently available—far lower than historical peaks—the systemic issues confronting the labor market introduce a sobering reality. It’s estimated that to return to a level of manufacturing employment reminiscent of 1979, around 22 million additional jobs would need to be created, an unlikely scenario given the present unemployment statistics.
Moreover, optimistic projections of a reshoring boom are further complicated by a lack of skilled labor, which hampers companies’ ability to expand their manufacturing footprint in the U.S. While companies like Nvidia and Apple have made substantial commitments to invest domestically, these announcements do not inherently translate to a sweeping revival of jobs in traditional manufacturing roles. The need for specialized skill sets in modern manufacturing means that simply relocating jobs is far more complex than it may appear on the surface. Wells Fargo underscores that the struggle to restore the manufacturing landscape signifies a significant challenge for both businesses and policymakers aiming to revitalize this sector.
The Future of U.S. Manufacturing Amidst Tariff Policies
As the landscape of U.S. manufacturing evolves, the impact of Trump’s tariffs will continue to shape strategic decisions within companies. Many industry leaders are wrestling with the dual pressures of maintaining competitive prices while navigating elevated operational costs spurred by tariffs. This precarious balance affects the overall manufacturing employment landscape, as companies weigh the benefits of domestic production against the economic realities of increasingly expensive labor and materials.
Looking forward, it’s essential for policymakers to tailor support strategies that not only target tariff adjustments but also prioritize workforce development. Initiatives that bolster skills training and educational programs for potential factory workers may help address labor shortages that hinder industry growth. Without a concerted effort to align workforce capabilities with the demands of modern manufacturing, even the most ambitious tariff policies may fall short of driving a significant resurgence in U.S. manufacturing jobs.
Understanding the Trade War’s Impact on Manufacturing Jobs
The trade war initiated under the Trump administration brought a significant shift in how U.S. companies approach international trade and manufacturing. With tariffs on key imports, firms have had to reassess their supply chains and manufacturing locations. Despite the intent to protect domestic jobs, many economists warn that these policies may inadvertently raise production costs, making U.S.-made goods less competitive in the global market, which could stifle the growth of manufacturing jobs rather than foster them.
Wells Fargo’s assessment indicates that while the tariffs may have short-term effects in certain sectors, the long-term outlook for U.S. manufacturing jobs remains bleak without substantive change. Companies may turn to automation or artificial intelligence to mitigate labor costs exacerbated by tariff-induced pricing pressures. Thus, the trade war’s ramifications extend beyond immediate job creation, influencing the broader trajectory of manufacturing employment and the adaptation to future technological advances.
The Role of Economic Policy in Manufacturing Growth
Economic policy plays a pivotal role in determining the health of the U.S. manufacturing sector. Tariffs are one lever among many that policymakers can use to influence manufacturing employment. However, the Wells Fargo analysis suggests that solely relying on tariffs is insufficient to achieve a thriving manufacturing landscape. A multi-faceted approach, including tax incentives, education policies, and infrastructure investments, will be crucial for nurturing the industry’s long-term viability.
Additionally, ongoing geopolitical tensions may further complicate policy approaches to manufacturing jobs. The landscape of global trade is constantly evolving, and manufacturers must adapt while also facing domestic challenges such as rising labor costs and limited job candidates. Thus, effective economic policy must not only address the immediate impacts of tariffs but also cultivate an environment conducive to sustainable growth in the manufacturing sector, ensuring that U.S. firms can compete successfully on the global stage.
Evaluating the Effectiveness of Tariff Strategies
Evaluating the effectiveness of tariff strategies, such as those implemented by the Trump administration, reveals a complex scenario for U.S. manufacturing. While the objective has been to create incentives for domestic job growth, the analysis from Wells Fargo suggests that the outcome may not align with these goals. Companies are experiencing increased operational costs due to tariffs, which limits their ability to hire and expand operations in the U.S.
Moreover, the effectiveness of these tariff strategies is further complicated by market reactions and global supply chain dynamics. Continued uncertainty regarding trade policies may deter firms from making significant commitments to reshoring or expanding manufacturing jobs domestically. This consideration emphasizes the need for a more holistic evaluation of tariff impacts, ensuring that policymakers take a comprehensive approach to bolster manufacturing while considering long-term sustainability.
The Workforce Imperative for Reshoring
Central to the challenge of bringing manufacturing jobs back to the U.S. is the workforce. The current labor market does not align with the needs of manufacturers who are looking to reshore operations. Wells Fargo highlights that despite the optimistic narrative surrounding reshoring driven by tariffs, there is a stark deficiency in workers with the necessary skills to meet modern manufacturing demands. Addressing this skill gap requires strategic initiatives focusing on education and training for the current and future workforce.
To truly capitalize on the potential of reshoring, companies and policymakers must collaborate to create pathways for individuals to acquire the relevant skills. This includes initiatives like apprenticeships, vocational training programs, and partnerships with educational institutions, which can help to prepare a workforce capable of supporting the diverse needs of the manufacturing sector. Only through targeted workforce development can the ambitions of growing U.S. manufacturing sustainable realize their full potential in the wake of tariff policies.
Insights from High-Profile Investments in Manufacturing
High-profile investments from technology giants such as Nvidia and Apple provide crucial insights into the future of U.S. manufacturing amid evolving tariff conditions. These companies have indicated commitments to expand domestic operations, which could serve as a catalyst for localized job creation in tech-driven manufacturing environments. While such investments do raise hopes for U.S. manufacturing growth, they also underscore the need for a nuanced understanding of labor dynamics and economic feasibility.
These corporate decisions are influenced by a range of factors, including the availability of a skilled labor pool, cost efficiency, and evolving consumer demands. While the significant financial commitments from these companies are promising, they do not automatically translate into widespread job growth in traditional sectors. Wells Fargo’s analysis indicates that the majority of manufacturing jobs lost may not be recoverable through these investments alone, highlighting the importance of strategic policy and investment that extends beyond mere announcements.
Navigating the Path Ahead for Manufacturing Employment
As we look ahead to the future of manufacturing employment in the U.S., it is essential to recognize the multidimensional challenges posed by tariffs and trade policies. The complexities of reviving U.S. manufacturing require an integrative approach that addresses economic, educational, and workforce readiness aspects. Wells Fargo’s insights serve as a reminder that while intentions behind tariffs may be noble, the practical implications on employment must be carefully navigated to achieve lasting results.
Ultimately, the path to a revitalized manufacturing sector lies in collaboration among stakeholders, including industry leaders, educational institutions, and policymakers. Building a robust, skilled workforce and creating a favorable environment for innovation and investment will be key to overcoming the existing hurdles in U.S. manufacturing. As companies continue to grapple with the on-the-ground realities of tariffs and labor shortages, combining policy measures with community engagement will yield the best results in shaping a sustainable future for manufacturing jobs.
Frequently Asked Questions
How do Trump tariffs affect U.S. manufacturing jobs?
Trump tariffs aim to incentivize the return of U.S. manufacturing jobs by increasing the cost of imports. However, an analysis from Wells Fargo indicates that these tariffs may not significantly boost manufacturing employment, as high labor costs and a tight job market present challenges for companies.
What does the Wells Fargo analysis say about the impact of Trump tariffs on reshoring jobs?
According to Wells Fargo’s analysis, while the Trump tariffs are designed to encourage reshoring, the financial and operational challenges companies face mean that a substantial increase in reshoring jobs is unlikely in the near future.
Are trade war tariffs effective in restoring manufacturing employment in the U.S.?
Trade war tariffs, including those implemented during Trump’s presidency, have not effectively restored manufacturing employment levels. The Wells Fargo report suggests that the cost of manufacturing in the U.S. remains too high for many firms to significantly expand hiring.
What is the current state of U.S. manufacturing jobs compared to historical levels?
As of now, there are approximately 12.8 million manufacturing jobs in the U.S., significantly lower than the 1979 peak of 19.5 million jobs. The Wells Fargo analysis emphasizes that reaching those historical levels again is a daunting challenge due to labor market constraints.
What are the expected outcomes of Trump’s tariffs on U.S. companies?
While Trump’s tariffs are intended to boost U.S. companies, Wells Fargo highlights that the resulting higher prices and uncertainty may hinder firms’ willingness to expand payrolls, limiting the anticipated resurgence in manufacturing employment.
Can Trump tariffs lead to a reshoring boom in U.S. manufacturing?
Although Trump tariffs are intended to spark a reshoring boom, the Wells Fargo analysis suggests that the increased costs of labor and production in the U.S. may dampen companies’ efforts to bring jobs back from overseas.
What role does the labor market play in the effectiveness of Trump tariffs?
The labor market plays a crucial role in the effectiveness of Trump tariffs. With only 7.2 million unemployed individuals available, the shortage of production workers poses a significant barrier to increasing U.S. manufacturing jobs, as noted in Wells Fargo’s analysis.
Key Point | Details |
---|---|
Trump’s Tariffs | Designed to incentivize manufacturing jobs back to the U.S. |
Labor Costs | Bringing back jobs would significantly increase labor costs, making it unaffordable for many companies. |
Tight Labor Market | Existing tight labor market for production workers complicates job growth. |
Future Job Growth | Wells Fargo predicts minimal increases in manufacturing jobs in the near future. |
Manufacturing Job Numbers | Currently at 12.8 million, significantly lower than the peak of 19.5 million in 1979. |
Impediments to Growth | Higher prices and policy uncertainty hinder expansion of payrolls. |
Reshoring Trend | Trump’s administration sees potential for reshoring, boosted by recent announcements from tech companies. |
Unemployment Rates | With only 7.2 million unemployed, reaching historical job levels seems unattainable. |
Summary
Trump tariffs are unlikely to revive U.S. manufacturing jobs to their peak levels due to rising labor costs and a tight labor market. The analysis from Wells Fargo suggests that the ambitious goal of bringing back millions of manufacturing jobs faces numerous challenges. Despite the administration’s optimism fueled by trade tariffs and incentives, the current job landscape indicates an uphill battle for restoring manufacturing employment in America.