US-China Tariff Challenges Impacting Holiday Supply Chains
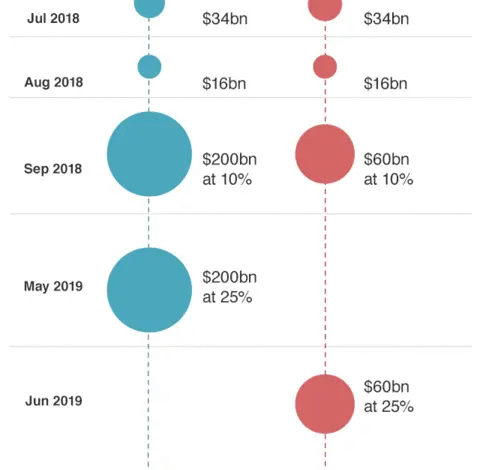
The ongoing US-China tariff challenges are creating significant hurdles for American retailers, especially as they prepare for the holiday season. As factories in China struggle with tariff uncertainties, the supply of Christmas merchandise is jeopardized, creating anxiety among those relying on timely electronic product shipping. Experts highlight that manufacturers must ship goods by early September to ensure they reach U.S. shelves in time for Thanksgiving, which amplifies the urgency surrounding inventory management. Moreover, the tariff impact on retailers has led many to reconsider their order strategies, opting to partially refill to avoid empty store shelves during peak shopping times. As businesses face the prospect of supply chain disruptions, the delicate balance of meeting consumer demand while navigating tariffs underscores the ongoing complexity of U.S.-China trade relations.
Navigating the intricate landscape of tariffs and trade policies between the U.S. and China has emerged as a pressing concern for businesses seeking to stock their holiday inventories. The complexities of import duties are largely influencing how retailers manage their supply logistics, particularly in relation to Christmas goods. Retailers are feeling the effects of these tariffs, as they strategically plan their orders for electronic items and other merchandise critical to the upcoming festive season. With the holiday shopping period on the horizon, the need for effective supply chain management is underlined by the unpredictable nature of tariff evaluations. This situation illustrates the broader implications for global trade dynamics, as companies actively seek ways to mitigate risks while ensuring product availability during peak consumer demand.
Understanding US-China Tariff Challenges
The ongoing US-China tariff challenges have become a significant concern for businesses involved in international trade, particularly in the lead-up to the holiday season. Tariffs imposed on Chinese imports, reaching up to 145%, have created a ripple effect throughout the supply chain, particularly for retailers relying on timely deliveries of Christmas merchandise. This heightened uncertainty forces many U.S. buyers to rethink their purchasing strategies, ultimately impacting the availability and pricing of products during the crucial holiday shopping season.
As U.S. importers navigate through these tariff-induced challenges, the implications extend well beyond the immediate cost increases. Many retailers are forced to adapt by diversifying their supply chains or reconsidering their inventory timelines, which is essential to minimize the risk of stockouts during key shopping periods. This shift in strategy focuses heavily on managing cash flow and ensuring that holiday season inventory matches consumer demand—something that is increasingly difficult due to the dynamic tariff landscape.
Impact of Tariffs on Retailers During the Holiday Season
The impact of tariffs on retailers during the holiday season cannot be overstated. With many businesses reliant on imported Christmas merchandise, the additional costs imposed by tariffs have forced them to evaluate their pricing strategies. Retailers must balance the need to remain competitive while absorbing the increased costs, leading to potential price hikes for consumers. This situation can create a challenging market environment, especially for smaller retailers who may lack the financial flexibility to weather prolonged tariff pressures.
Furthermore, the shifting landscape of tariff evaluations creates a climate of uncertainty. Retailers often hesitate to place larger orders in anticipation of potential tariff relief or further increases, which could leave shelves empty during peak shopping periods. The hesitation to commit to inventory replenishment underscores the fragility of supply chain operations in a tariff-driven economy, making it critical for U.S. retailers to remain agile in managing their merchandise orders.
Navigating Supply Chain Disruptions for Holiday Merchandise
Supply chain disruptions pose a significant hurdle as retailers prepare for the critical holiday shopping period. The timeline for importing electronic products and other holiday goods extends into complex planning processes that are now compounded by tariff uncertainties. With six months required for a typical product to transition from production in China to being available on U.S. shelves, timing becomes crucial for retailers looking to stock their stores in advance of key shopping days like Black Friday and Christmas.
To mitigate the effects of these disruptions, many businesses are adopting innovative strategies, such as diversifying their supplier base and reevaluating their shipping routes. Some retailers are now considering alternative sourcing locations to reduce dependency on Chinese suppliers, while still striving to maintain quality and cost-effectiveness. This tactical approach not only aims to counterbalance tariff implications but also focuses on creating a more resilient and flexible supply chain capable of adapting to future shocks.
The Role of Electronic Products in Holiday Inventory Planning
Electronic products are a cornerstone of holiday gift-giving, making their timely arrival in U.S. markets essential for retailers. The necessity for early shipping dates, ideally by early September, puts additional pressure on both Chinese manufacturers and their U.S. partners to synchronize their production timelines effectively. As businesses prepare for the holiday season, understanding the intricate relationship between tariffs, production schedules, and shipping logistics is vital to ensuring sufficient inventory is available to meet consumer demands.
Additionally, the unpredictability of tariffs adds an extra layer of complexity to the management of electronic product shipments. Retailers must closely monitor external factors that could influence pricing and availability, necessitating collaborative efforts between factories and distribution networks. Forward-thinking businesses are already strategizing ways to streamline their operations, indicating an urgent need to adapt extensively to the changing market dynamics.
Shipping Strategies in Light of Tariff Uncertainty
The shipping strategies employed by retailers are experiencing a paradigm shift influenced by ongoing tariff uncertainty. As businesses brace for potential increases in shipping costs and interruptions in their supply chains, there has been a noticeable trend toward more strategic planning. This includes anticipating delays in shipments and finding ways to mitigate these risks, such as securing shipping containers well in advance.
Moreover, by employing technology and data analytics, businesses can gain valuable insights into shipping trends and better track their inventory movements. This data-driven approach allows retailers to optimize their shipping schedules and maintain a consistent flow of merchandise, which is particularly vital during the high-stakes holiday season where demand peaks.
Strategies to Minimize Tariff Impacts on Seasonal Inventory
In a climate fraught with tariff-related challenges, U.S. retailers are devising various strategies to minimize impacts on their holiday inventory. One common approach involves placing contingent orders, where businesses secure goods based on potential tariff relief outcomes. By creating flexible agreements with suppliers, retailers can adapt their orders based on the evolving tariff situation to safeguard their margins better while ensuring they meet consumer needs during the critical holiday shopping window.
Additionally, precise inventory management plays a critical role in success during the holiday season. Retailers are leveraging inventory analytics tools to gain real-time insights into stock levels and customer demands. This proactive strategy not only helps reduce excess inventory but also empowers businesses to respond promptly to shifts in supply chain dynamics, allowing for a more agile response to market changes driven by tariffs.
Adjusting to Evolving Import Regulations
As import regulations continue to evolve, retailers must remain vigilant in adapting their import practices to align with changing tariff structures. The implementation of new regulations can have far-reaching implications for how companies approach their international sourcing strategies, particularly in terms of costs and lead times. By being proactive in scrutinizing these regulations, businesses can identify potential areas of opportunity to lower their overall tariff burdens.
Additionally, engaging with legal and trade experts can provide retailers with clarity regarding the complexities of import regulations, allowing them to make informed decisions about their sourcing and inventory strategies. This strategic partnership can lead to more efficient operations while ensuring compliance with ever-changing trade policies, thereby enhancing competitiveness in the marketplace.
The Future of US-China Trade Relations and Holiday Preparations
As we look towards the future of US-China trade relations, it is evident that ongoing tariff negotiations will shape the landscape for retailers as they prepare for future holiday seasons. The interconnectedness of supply chains highlights how changes in trade policies can quickly ripple through various sectors. Retailers will need to stay informed and adaptable, positioning themselves strategically to navigate potential trade fluctuations.
In light of these factors, maintaining open communication channels with suppliers and logistics partners remains necessary for tackling the uncertainty surrounding global trade. By fostering strong relationships within the supply chain, retailers can enhance their resilience and preparedness for upcoming holiday seasons, ultimately securing their market position amid ongoing economic challenges.
Leveraging Technology to Counteract Tariff Effects
In the age of digital transformation, leveraging technology is becoming an increasingly common strategy for retailers to counteract tariff effects on supply chains. Advanced analytics, cloud computing, and AI-driven forecasting tools provide businesses with the capability to analyze market trends and consumer behavior, enabling them to make more informed inventory decisions.
With technology streamlining operations from production to customer delivery, businesses can enhance their visibility into supply chain workflows. This holistic view allows retailers to identify inefficiencies and mitigate risks associated with tariffs, ensuring they can adapt swiftly to any market changes that may arise during peak shopping seasons.
Frequently Asked Questions
How are US-China tariff challenges affecting Christmas merchandise supply for the 2023 holiday season?
US-China tariff challenges are significantly impacting Christmas merchandise supply for the 2023 holiday season. Tariffs on imports from China, particularly those imposed during the previous administration, have led U.S. retailers to reduce orders and halt production at local factories. This disruption is threatening timely stock availability for the Christmas season, as businesses strive to manage inventory effectively amid tariff uncertainties.
What is the tariff impact on retailers for electronic products in the upcoming holiday season?
The tariff impact on retailers for electronic products is profound, with many facing increased costs due to tariffs on Chinese imports. Retailers are now cautious about their orders, ensuring they stock up on inventory before potential further tariff evaluations. As these tariffs increase, the pressure on profit margins also rises, compelling retailers to reconsider their shipping schedules and product availability.
What are the implications of supply chain disruptions due to tariffs on holiday season inventory?
Supply chain disruptions caused by tariffs have critical implications for holiday season inventory. Many U.S. retailers are experiencing delays in receiving goods due to cautious ordering practices in light of potential tariff changes. This has led to a sharp decline in shipping volumes from China, ultimately affecting the availability of holiday merchandise just in time for shopping events like Black Friday and Christmas.
How can US-China tariff challenges affect the shipping of electronic products?
US-China tariff challenges complicate the shipping of electronic products by increasing shipping costs and creating uncertainty in timelines. Businesses must ensure that products are shipped by early September to hit holiday sales targets, adding urgency to their order placement. Any delays in the shipping process could result in missed sales opportunities during key shopping seasons.
What strategies are U.S. retailers employing to cope with holiday season inventory challenges caused by tariffs?
To cope with holiday season inventory challenges imposed by tariffs, U.S. retailers are carefully balancing their ordering strategies. Some are partially refilling orders to maintain stock without overwhelming their supply chains. Additionally, retailers are staying informed about tariff evaluations and adjusting production timelines accordingly to ensure they can meet consumer demand during the holiday season.
Why is timing production important for U.S. businesses facing US-China tariff challenges?
Timing production is critical for U.S. businesses facing US-China tariff challenges, as delays can lead to significant shortages in holiday inventory. With estimates saying that it takes about six months from production to store shelves, businesses must act quickly to avoid being caught off-guard by tariff shifts. Planning ahead and aligning production with anticipated tariff changes is essential for maintaining a competitive edge during the holiday season.
How are U.S. buyers responding to the ongoing US-China tariff challenges ahead of the holiday season?
U.S. buyers are responding to ongoing US-China tariff challenges by adopting a cautious approach. Many are waiting for clearer tariff evaluations before making new orders, while some are speculating on potential tariff relief and adjusting their production plans accordingly. This cautious strategy reflects a need to navigate the uncertainty in the supply chain while still preparing for the demanding holiday shopping period.
What is ‘Christmas creep’ and how do US-China tariffs influence its occurrence?
‘Christmas creep’ refers to the trend where retailers start stocking holiday merchandise earlier to capture consumer spending. US-China tariffs have influenced this phenomenon by creating uncertainty in supply chains, prompting retailers to begin stocking earlier to ensure availability despite potential delays. This strategy becomes particularly important as they aim to mitigate risks associated with tariffs and supply disruptions.
How are shipping trends from China to the U.S. changing amid US-China tariff challenges?
Shipping trends from China to the U.S. are showing a marked decline amid US-China tariff challenges, with fewer container ships departing for the U.S. than previous years. This reduction reflects a downturn in exports as businesses become more selective about their orders, preemptively managing risks associated with tariff impacts and inventory shortages as the holiday season approaches.
What are the risks for U.S. retailers if they do not adapt to US-China tariff challenges during the holiday season?
If U.S. retailers do not adapt to US-China tariff challenges during the holiday season, they risk facing empty shelves, lost sales opportunities, and heightened competition. Delays in production and shipping could lead to a significant shortfall in holiday inventory, potentially resulting in diminished customer satisfaction and lasting impacts on brand loyalty.
Key Points | Details |
---|---|
Tariff Uncertainty | Chinese factories and U.S. buyers face uncertainties due to tariffs on Christmas merchandise. |
Shipping Deadlines | Electronic products must be shipped by early September to ensure availability for Thanksgiving. |
Impact on Orders | Some businesses are filling orders cautiously to prevent empty shelves. |
Christmas Creep | Early stocking of holiday goods may be hindered by tariffs. |
Production Challenges | U.S. retailers’ order cessation led to local factory production halts. |
Rerouting Goods | Replacing supply chains is complex; 36% of U.S. imports still depend on China. |
Timing Issues | Order timing is critical; manufacturers need to act quickly to avoid holiday stockouts. |
Inventory Stockpiling | Buyers stockpiled inventories prior to expected tariff evaluations. |
Market Caution | Some buyers are hesitant to place new orders until tariff evaluations are complete. |
Summary
The US-China tariff challenges have significantly affected the trade dynamics as businesses grapple with the implications of these tariffs on their operations. As the holiday season approaches, the pressure mounts on supply chains to adapt promptly to ensure product availability. The complexity of modern supply networks, alongside the unpredictability of tariff environments, underscores the need for businesses to navigate these challenges with strategic foresight.