China Reduces US Treasury Holdings Amid Trade War
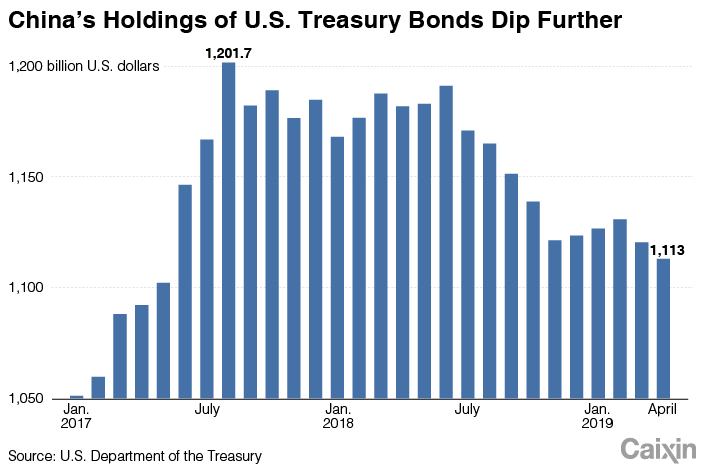
China reduces US Treasury holdings, reflecting a significant shift in its approach to U.S. debt amid escalating trade tensions. In March, China sold nearly $19 billion of its U.S. Treasury securities, a move that has sparked discussions around the implications for China US trade relations and the overall health of the US Treasury bond market. With its holdings slipping to $765.4 billion from $784.3 billion just a month prior, concerns mount regarding the potential trade war impact on debt, especially as America’s financial stability becomes a focal point for investors. This strategic maneuver has led China to drop to third place among the largest holders of U.S. Treasury debt, now surpassed by the U.K. and Japan. Furthermore, the recent downgrade of the U.S. credit rating by Moody’s illuminates the growing apprehension about the sustainability of U.S. debt amidst the ongoing tariff conflict.
The recent decision by Beijing to trim its investments in U.S. government bonds marks a notable transition in its financial strategy. As the trade war intensifies, China appears to be recalibrating its approach to American debt, signaling broader implications for international finance. This development, where China’s Treasury holdings have notably decreased, raises questions about the future of global debt markets and the dynamics of China US relations. With increased volatility surrounding American financial assets, stakeholders are eyeing the ramifications of such liquidity contraction, while experts grapple with the potential reverberations in economic confidence. The intersection of geopolitical tensions and financial markets underscores the complexity of these evolving scenarios.
Impact of China Reducing US Treasury Holdings
The recent decision by China to reduce its holdings in U.S. Treasuries has raised concerns about the overall stability of the U.S. Treasury bond market. With China selling nearly $19 billion in March alone, this move underscores the growing unease regarding U.S.-China relations amid a protracted trade war. This significant divestment not only signals a shift in foreign investor confidence but also places additional pressure on U.S. borrowing costs, potentially leading to higher interest rates for consumers and businesses alike.
This adjustment in China’s U.S. Treasury holdings can also be interpreted as a strategic maneuver to mitigate risks associated with holding debt from a nation facing escalating trade tensions. The drop in holdings from $784.3 billion to $765.4 billion reflects a broader reassessment of how foreign entities prioritize their portfolios in light of potential geopolitical fallout. As analysts comme nt on the implications of this decline, many suggest that it signals a need for the U.S. to enhance its creditworthiness and stability to retain international investors.
Trade War’s Influence on China’s Debt Strategy
The ongoing trade war between the U.S. and China has become a pivotal factor influencing China’s approach to its debt investments. Initially, in February 2023, contrary to expected patterns during the trade conflict, China actually increased its Treasury holdings by over $20 billion. This behavior was surprising, as many anticipated a sell-off in response to heightened tensions. However, it appears to have been a temporary strategy to potentially leverage bargaining power before the tariffs escalated further.
As the trade war intensified, particularly with tariffs reaching critical levels, China’s subsequent reduction in U.S. Treasury holdings indicates a shift toward a more cautious investment stance. This evolution in strategy reflects a broader trend where nations adjust their foreign reserves to safeguard against potential economic fallout from tariffs and trade disputes. The dynamic nature of these relations highlights the interconnectedness of global finance, as shifts in one country’s policy have the potential to ripple through global markets and affect other sovereign debt investors.
Moody’s Credit Rating Downgrade and its Effects
The recent downgrade of the United States’ credit rating by Moody’s from ‘AAA’ to ‘Aa1’ plays a critical role in the context of China’s reduced exposure to U.S. debt. This downgrade, attributed to escalating government debt levels over the past decade, has raised alarms among investors. With interest payments and debt ratios becoming increasingly unsustainable, foreign investors like China may reconsider the potential risks and returns of holding U.S. debt, especially during turbulent economic times.
Furthermore, the downgrade signifies more than just a change in rating; it reflects declining confidence in U.S. fiscal policy and the government’s ability to manage its debt obligations effectively. As a result, China’s divestment from Treasuries could be seen as a proactive measure to decrease vulnerability associated with holding assets that could potentially lose value in the wake of further downgrades. This sentiment resonates with financial analysts who speculate that if the U.S. does not stabilize its debt levels, it may face more significant repercussions in global finance.
China’s Position in the US Treasury Landscape
With China recently falling to third place among the largest holders of U.S. Treasuries, it has ceded its previous position to the United Kingdom as a result of its ongoing divestment strategy. This shift has profound implications for the U.S. economy, given that foreign investment plays a crucial role in sustaining financial stability. The competition now intensifies as Japan retains its status as the largest holder of U.S. debt, raising questions about how these changes will affect broader U.S.-China trade relations.
China’s strategy to reduce its U.S. Treasury holdings illustrates a clear shift towards risk management in an uncertain economic climate. As different nations adjust their portfolios in response to geopolitical factors such as tariffs and trade policies, the pressure on the U.S. Treasury market could mount. Each decision made by foreign financiers like China serves to highlight the complex interplay between international economics and national policy, further complicating the already fraught U.S.-China relationship.
Risk Management Amidst the Trade War
In light of the escalating trade war between China and the United States, risk management has emerged as a crucial theme in China’s approach to its U.S. Treasury holdings. By strategically reducing its debt position amidst concerns about default risk and geopolitical tensions, China is taking steps to preserve the integrity of its foreign reserves. This proactive stance may also be a reflection of internal assessments regarding the potential long-term ramifications of the trade dispute.
As the trade war continues to unfold, analysts suggest that China’s divestment represents a calculated approach to shield its economy from the adverse effects of an increasingly volatile relationship with the U.S. This calculated risk aversion could sway other investors to reconsider their exposure to U.S. debt, thus creating a ripple effect in the global financial landscape. Moving forward, both nations may need to reassess their strategies to foster more stable economic interactions.
Future of US Treasury Bond Market amid Trade Tensions
Given the current geopolitical tensions and the actions of nations like China in response to the trade war, the future of the U.S. Treasury bond market appears uncertain. With a decline in foreign holdings, particularly from significant players like China, the demand for U.S. Treasuries may wane, leading to increased borrowing costs for the U.S. government. A downward spiral in demand could have broader implications, affecting funding for various public programs and infrastructure projects.
Moreover, as nations navigate the delicate balance between trade relations and financial investments, the U.S. Treasury must adapt to these changing dynamics to reinforce confidence among investors. Efforts to stabilize debt levels and further improve fiscal policies will be imperative in maintaining a robust bond market. Addressing these issues will not only impact domestic markets but would also play a vital role in shaping international investor attitudes towards U.S. debt.
Analyzing the Consequences of China’s Strategy
The consequences of China’s strategic reduction in U.S. Treasury holdings are multifaceted and warrant thorough analysis. As China takes a step back from its once-heavy investment in U.S. debt, it necessitates a reevaluation of the potential impacts on U.S. financial markets. Expectations of rising interest rates due to declining demand for Treasuries could surge, resulting in higher costs for both consumers and businesses that rely on loans and credit.
Furthermore, China’s shift emphasizes the growing risk-awareness among global investors as trade tensions persist. This behavior suggests a longer-term strategy focused on safeguarding economic interests amidst volatility, thus motivating other nations to reconsider their own dependencies on U.S. debt. The evolving global landscape indicates a need for countries to develop diversified portfolios, reflecting broader trends in international finance as trade strategies evolve.
Global Repercussions of China’s Holdings Adjustment
The adjustment of China’s U.S. Treasury holdings extends beyond bilateral implications, creating global reverberations. As perceptions about the U.S. creditworthiness fluctuate—especially following Moody’s downgrade—other countries holding U.S. Treasury bonds may also rethink their portfolios. A collective shift away from U.S. debt by multiple nations could undermine the dollar’s status as the world’s reserve currency, instigating a profound realignment in global economic power.
Moreover, as nations such as China adjust their financial behaviors, this can potentially impact emerging markets that rely on U.S. economic stability. Investors worldwide will closely monitor these movements, as a decrease in demand for U.S. Treasuries could provoke instability in a range of sectors, highlighting the interconnectedness of global financial systems. Understanding these complexities is essential as nations navigate their economic policies amidst ongoing challenges.
China and the Future of US-China Financial Relations
The trajectory of U.S.-China financial relations is at a critical juncture, particularly as China reassesses its holdings in U.S. Treasuries amid the tension of the trade war. Each strategic financial decision indicates deeper undercurrents regarding the stability and cooperation between the two nations. The current trend of reducing debt exposure could signify a long-term shift towards competitive financial positioning rather than cooperative development.
Looking ahead, the future of economic interactions between the U.S. and China will hinge on their ability to navigate the complexities of mutual dependency and competitive aspirations. Establishing a stable framework for negotiations, including trade and financial policies, will be essential. Both countries must efficiently address existing tensions, or risk enduring a cycle of retaliatory measures that harm economic interests on both sides.
Frequently Asked Questions
Why is China reducing its US Treasury holdings amid the trade war?
China is reducing its US Treasury holdings as a strategic response to the ongoing trade war. In March, China sold approximately $19 billion in US Treasuries, decreasing its holdings to $765.4 billion. This reduction reflects concerns about the potential risks of holding US debt, especially given the trade conflict escalating tariffs and retaliation measures.
What impact does China’s reduction of US Treasury debt have on the US bond market?
China’s reduction of US Treasury debt could significantly impact the US bond market by decreasing demand for US Treasuries. As one of the largest creditors, China’s selling of nearly $19 billion in Treasuries adds downward pressure on bond prices, which could lead to rising interest rates if demand cannot keep pace with supply.
How do trade relations between China and the US affect US Treasury bond holdings?
The trade relations between China and the US directly influence China’s US Treasury bond holdings. As tensions escalated during the trade war, marked by tariffs and economic retaliation, China opted to reduce its exposure to US debt. This strategic move aims to mitigate financial risk associated with holding assets in a country facing potential defaults due to increased government debts.
What does Moody’s credit rating downgrade mean for US Treasury debt and China’s holdings?
Moody’s credit rating downgrade from ‘AAA’ to ‘Aa1’ for US Treasury debt indicates rising concerns about the sustainability of US government debt levels. This downgrade could lead to increased skepticism among foreign investors, including China, about the safety of US Treasury holdings, prompting further reductions in their investment in US debt amid fears of future defaults.
What were the trends in China’s US Treasury holdings before the trade war escalated?
Before the trade war escalated, China’s trends in US Treasury holdings showed fluctuations; for instance, in February, right before tensions rose, China increased its holdings by over $20 billion. This prior increase seemed counterintuitive amidst rising tariffs but highlighted a complex strategy that changed quickly as the trade environment became more hostile.
Is there a risk for China in reducing its US Treasury debt?
Yes, there are risks for China in reducing its US Treasury debt. While decreasing holdings can mitigate exposure to potential risks from the US economy, it also may lead to a loss of influence over US monetary policy and disrupt a vital source of liquidity. A hasty reduction could also trigger volatility in financial markets and negatively impact China’s own economic stability.
How might the future of US-China trade relations affect US Treasury holdings?
The future of US-China trade relations will likely play a crucial role in shaping US Treasury holdings. If tensions remain high and the conflict continues, it may lead China to further reduce its holdings in US debt. Conversely, improved trade relations could restore confidence and stabilize China’s investments in US Treasuries, ensuring bilateral economic cooperation.
Key Points | Details |
---|---|
China Reduces Holdings | In March 2023, China sold about $19 billion in U.S. Treasuries, reducing its holdings to $765.4 billion. |
Trade War Influence | The reductions align with the ongoing trade war and increase concerns over U.S. debt reliability. |
Position Among Holders | With the sell-off, China fell to the third largest holder of U.S. Treasuries, behind the U.K. and Japan. |
Market Implications | Chinese analysts believe these moves are precautionary against the risk of U.S. default amid trade tensions. |
Moody’s Rating | Moody’s downgraded U.S. debt from ‘AAA’ to ‘Aa1’, citing rising government debt and interest ratios. |
Summary
China reduces US Treasury holdings as part of its strategy to navigate the complexities of the ongoing trade war with the United States. The significant reduction in March highlights China’s concerns regarding the reliability of U.S. debt amidst escalating tariffs and economic tensions. In light of these developments, it is crucial for investors and policymakers to monitor China’s actions closely, as they could have substantial implications for global markets.